3D Printing is a valuable tool for designers and in rapid production.
General Motors took the time this week to offer details on how the company uses 3D printing in the manufacturer of low-volume vehicles, and how that technology offered great flexibility when GM shifted to producing much-needed medical equipment.
“3D printing helps us design and build parts and products faster and in ways we previously couldn’t,” said Kevin Quinn, GM director of additive design and manufacturing. “It’s already having a positive impact on how we develop and build vehicles, like Corvette, and it’s allowed us to apply our mass production expertise to medical supplies and devices.”
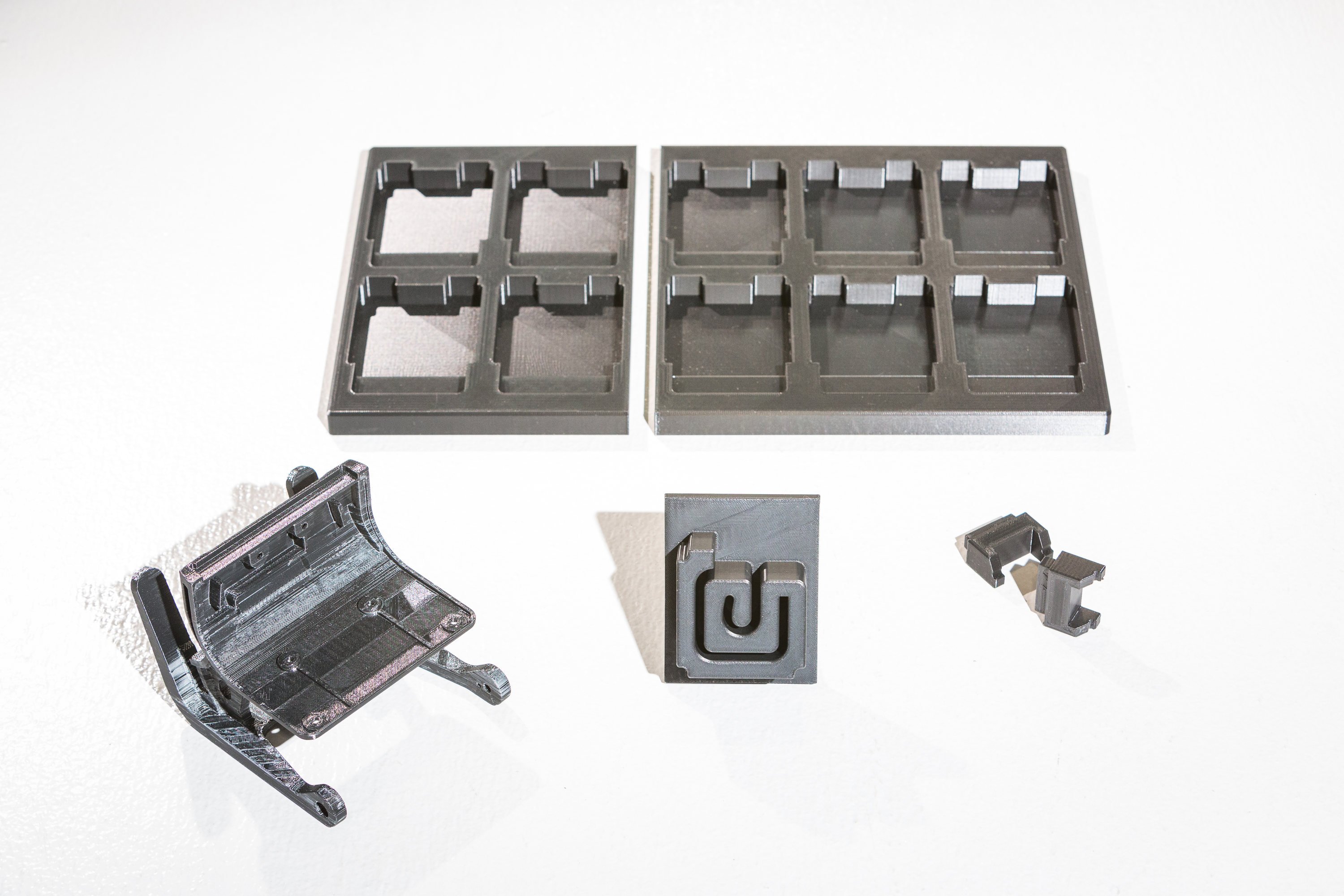
3D printing is an evolution of computer-aided design (CAD). In modern engineering and production, parts are “drawn” using software. That software can not only create a line drawing or 3D view of a part, it can export that file to a machine that can actually create it.
Many journalists who have not worked in engineering misunderstand the true value of 3D printing. Its best use is in the design, testing, and prototyping stages. For example, GM says that first time a physical version of the mid-engine Corvette came together, 75 percent of the parts were 3D printed. No previous GM “slow build” design and engineering evaluation has featured this amount or level of detail in terms of its 3D-printed components. This allowed the GM design team to envision what a production vehicle would look like and how all the parts would fit together. GM’s engineers were also able to diagnose and correct issues early on, reducing development time.
By allowing a team of designers and engineers to create physical parts rapidly, and to then alter the design and create a new version very quickly, 3D printing saves considerable time when a product is being developed. This skillset also allows a design and development team to quickly shift from one type of project to an entirely new project with great speed. This is one reason why GM could produce medical equipment in such a short time when called upon to do so.

In the real world, it is the product samples created by 3D printers that are perhaps most valuable. GM’s design team quickly delivered prototypes made with 3D printers to local healthcare workers and from there, made three crucial improvements based on healthcare workers’ feedback before producing face shields in large quantities.
“We could not have responded to the coronavirus as quickly as we did without 3D printing,” said Ron Daul, GM director of additive manufacturing. “The investment in both our additive manufacturing facilities and training the team to leverage 3D printing for development has enabled us to pivot to making ventilators and personal protective equipment virtually overnight.”
3D printing cannot produce all final versions of machine or product components. This is because 3D printers don’t print many needed materials. For example, a 3D printer cannot print a woven textile. Nor can a 3D printer print a metal alloy with the needed strength to perform most duties. However, models of the parts can be made, and made almost instantly.
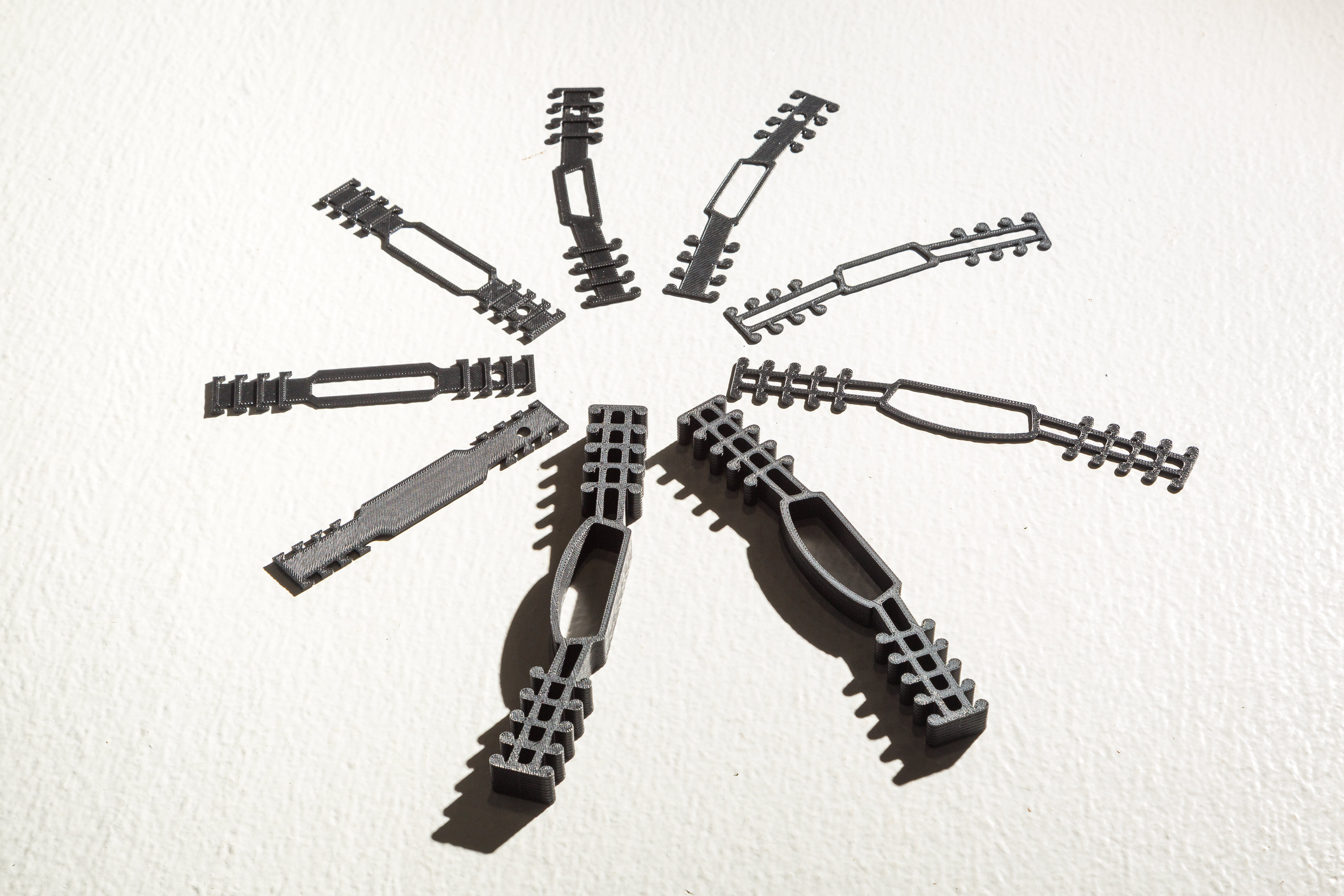
Some parts can be made of printable materials. Particularly parts that don’t need high tensile strength. For example, GM actually prints some parts of face shields for medical use. GM used the example of ear protectors what the team produces with its printers.
3D printers help most in the design and development of parts and products. They are not the most cost-effective way to produce high volumes of most parts. Nor are 3D printers able to create final versions of many parts that play roles requiring strength or durability.
GM is one of the few companies that has taken the time to clearly explain the true role of this important technology. The next time you read a story saying that your next car will be “made with a 3D printer,” this is the true story behind how the 3D printer is helping.